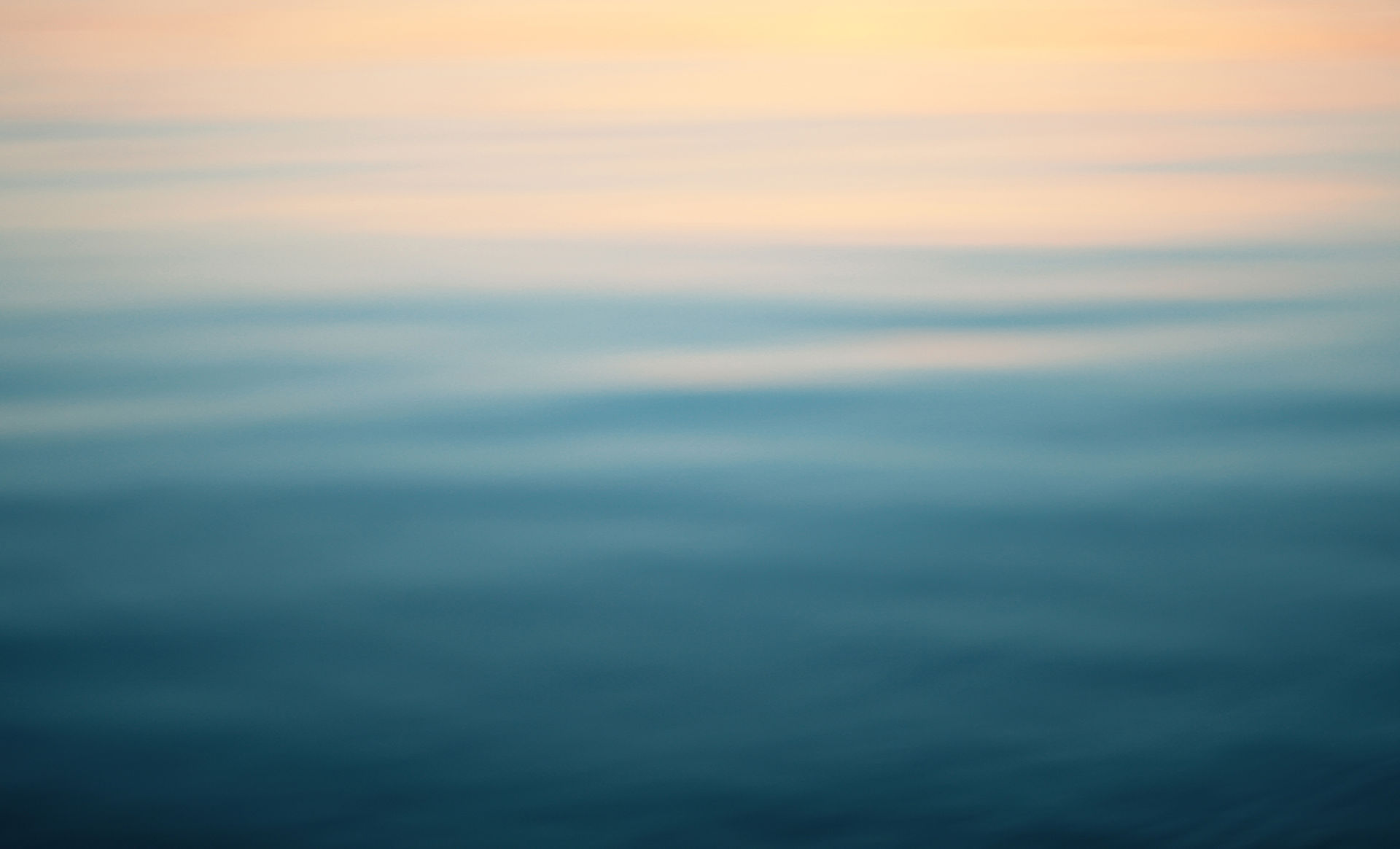

GESTIÓN DE CALIDAD
El Control Estadístico de la Calidad y la mejora de procesos.
Comenzando con la aportación de Shewhart sobre reconocer que en todo proceso de producción existe variación (Gutiérrez:1992), puntualizó que no podían producirse dos partes con las mismas especificaciones, pues era evidente que las diferencias en la materia prima e insumos y los distintos grados de habilidad de los operadores provocaban variabilidad. Shewhart no proponía suprimir las variaciones, sino determinar cuál era el rango tolerable de variación que evite que se originen problemas.
Para lograr lo anterior, desarrolló las gráficas de control al tiempo que Roming y Dodge desarrollaban las técnicas de muestreo adecuadas para solamente tener que verificar cierta cantidad de productos en lugar de inspeccionar todas las unidades. Este periodo de la calidad surge en la década de los 30’s a raíz de los trabajos de investigación realizados por la Bell Telephone Laboratories.
En su grupo de investigadores destacaron hombres como Walter A. Shewhart, Harry Roming y Harold Dodge, incorporándose después, como fuerte impulsor de las ideas de Shewhart, el Dr. Edwards W. Deming (Cantú:1997).
Estos investigadores cimentaron las bases de lo que hoy conocemos como Control Estadístico de la Calidad (Statistical Quality Control, SQC), lo cual constituyó un avance sin precedente en el movimiento hacia la calidad.
-
Las 7 herramientas estadísticas de la Calidad
La calidad de un producto o servicio se puede determinar por sus características de calidad, como, por ejemplo: acabado, dimensiones, estética, tiempos de entrega, etc.
Para establecer la calidad del producto se realizan mediciones de estas características y se obtienen datos numéricos. Lo habitual es que estos datos presenten pequeñas variaciones de un producto a otro. El análisis de estos datos nos aportará una información valiosa sobre el funcionamiento y eficacia de los procesos que nos permitirá estudiar y corregir cualquier desviación detectada.
Para analizar estos datos se hace necesario recurrir a técnicas estadísticas que permitan visualizar y tener en cuenta la variabilidad a la hora de tomar las decisiones. Existen multitud de técnicas y herramientas a este respecto, siendo las más conocidas “las siete herramientas de la Calidad”.
Estas siete herramientas fueron recopiladas en los años sesenta por Kaoru Ishikawa y la experiencia ha demostrado que el uso de estas sencillas herramientas permite resolver el 80% de los problemas que se presentan en las organizaciones.
La hoja de recogida de datos.
también llamada “hoja de registro”, consiste en un documento donde se pueda recoger de forma fácil y estructurada todo tipo de datos para su posterior análisis. En función de los datos a recoger, se diseña la hoja y se apuntan los datos indicando la frecuencia de observación.
Las hojas de recogida de datos pueden servir para recoger datos de:
- Localización de defectos de productos.
- Causas de los defectos.
- Clasificación de productos defectuosos.
- Variación de las características de los productos (dimensiones, peso, acabado, etc.).
Etc.
Y permite observar:
-Número de veces en el que sucede algo.
-Tiempo necesario para que algo suceda.
-Costo de una determinada actividad, a lo largo de un cierto periodo de tiempo.
-Impacto de una actividad a lo largo de un período de tiempo.
Diagrama de Pareto
El diagrama de Pareto es una forma de representar los datos en un gráfico de frecuencias, de manera que los datos aparecen ordenados de mayor a menor. Así se pueden identificar las principales causas de la mayor parte de los efectos producidos.
Según este concepto, si se tiene un problema con muchas causas, podemos decir que el 20% de las causas resuelven el 80% del problema.
El diagrama de Pareto es de gran utilidad para identificar y dar prioridad a los problemas más significativos de un proceso.
Recuerda que:
Las hojas de recogida de datos pueden servir para recoger datos de:
La minoría de los clientes que representan la mayoría de las ventas.
La minoría de los productos, procesos, o características de la Calidad causantes de la mayoría de los costos por las no conformidades.
La minoría de los rechazos que representan la mayoría de las quejas de los clientes.
La minoría de los problemas causantes de la mayor partes de los retrasos de un proceso.
La minoría de los productos que representan la mayoría de los beneficios obtenidos.
Diagrama de dispersión
El diagrama de dispersión o de correlación es una representación gráfica que nos permite estudiar si existe una relación entre dos variables. Este diagrama puede resultar de gran utilidad para la solución de problemas en un proceso, ya que nos permite comprobar qué causas (factores) están influyendo o perturbando la dispersión de una característica de calidad o variable del proceso a controlar.
De la forma en que se hallan dispersos los puntos obtenidos en el diagrama se puede obtener diferente información, siendo las formas más comunes (véase la Figura 9.10):
Correlación lineal positiva: al aumentar el valor de una variable, aumenta el de la otra.
Correlación lineal negativa: cuando aumenta una variable, la otra disminuye.
De correlación no lineal: existe relación entre las dos variables en forma de curva.
Sin correlación: no existe relación alguna de influencia entre las dos variables.
Diagrama causa-efecto
En general se puede afirmar que no existe ningún proceso que no esté sometido a variaciones. Es decir, el resultado del proceso nunca es el mismo. Si las variaciones son pequeñas y no afectan de forma significativa al resultado, podremos decir que el proceso funciona de forma estable y controlada y con gran capacidad (no se producen productos no conformes). Ahora bien, cuando estas variaciones son significativas y afectan a las características de calidad del producto, será necesario estudiar cuáles son las posibles causas de tales variaciones para poder reducirlas o eliminarlas.
El diagrama de causa-efecto, también conocido como diagrama de espina de pescado, por la forma que adopta, es una herramienta que nos ayuda a estudiar de forma estructurada todas las posibles causas que pueden producir variaciones en un proceso.
Por lo general, las causas más comunes que pueden ocasionar variaciones en los procesos son (las 6 M):
Variaciones en las Máquinas o equipos (las máquinas producen variaciones demasiado intensas)
Variaciones en el Material de entrada al proceso (la materia prima utilizada no es uniforme)
Variaciones en el Método o procedimiento (se aplican procedimientos de trabajo diferentes)
Variaciones en los operarios o Mano obra (las personas trabajan de forma diferente)
Variaciones en el Medio ambiente (el medio ambiente afecta al proceso)
Variaciones en las Medidas (fallos en el sistema de medida)
Diagrama de flujo
Esta sencilla herramienta, que ya conocemos, nos permite representar, de forma sencilla y gráfica, la secuencia que se produce en un proceso. Con el diagrama de flujo obtenemos una visión general del sistema y cómo se relacionan todos los elementos que lo componen. Es una herramienta muy útil para analizar un proceso y estudiar la manera de simplificarlo, mejorarlo y resolver todos aquellos problemas que se presenten.
La figura 9.14 representa un diagrama de flujo sencillo de la secuencia de actividades que se realizan cuando se va a arrancar el motor de un automóvil, e indica las posibilidades en el caso de que el motor no arranque.
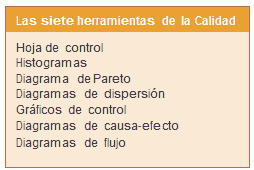
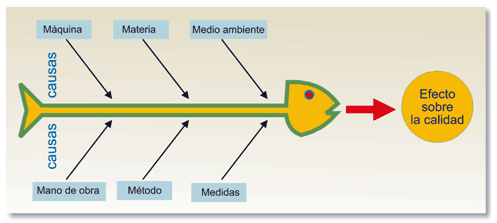
